How to Conduct a Workplace Safety Audit
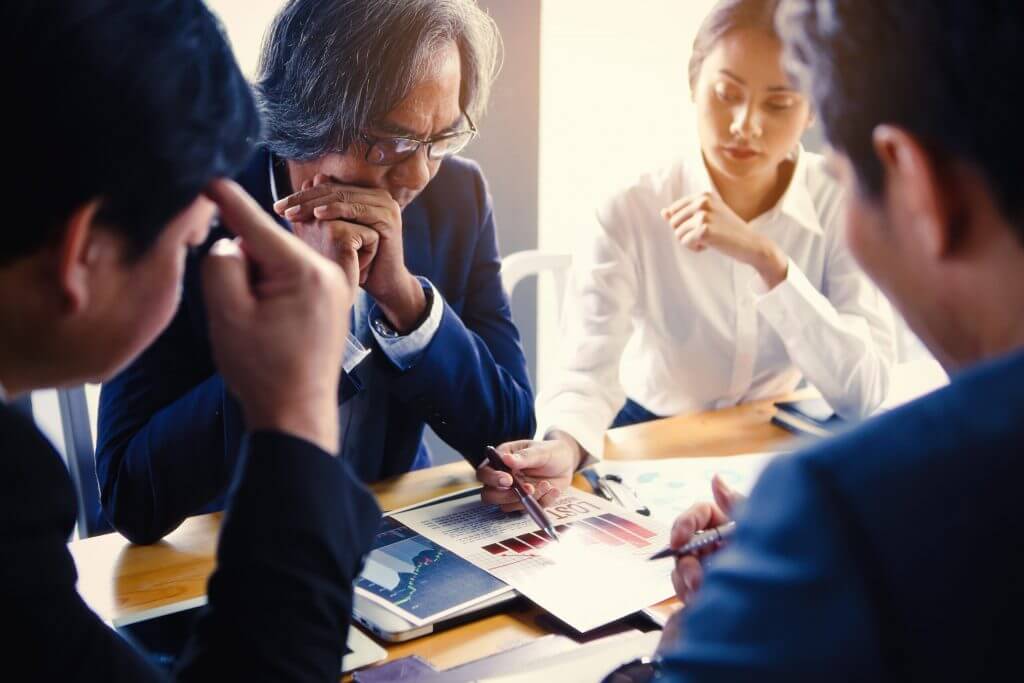
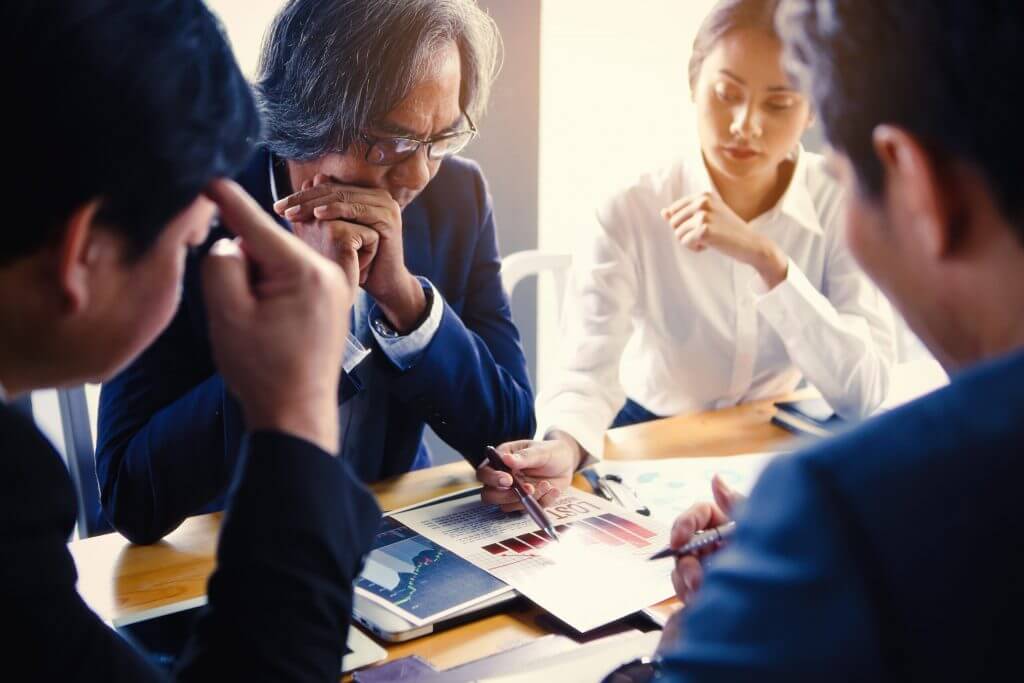
The aircraft of your organization will take off only if all its components (your employees) work in sync, with all their strengths. Sadly, however, workplace safety is an aspect that often hides away in the forgotten corners of organizations. The fact is, the safety of your employees is inextricably linked with a winning company’s bottom line.
From worker participation to hazard prevention to the involvement of management leadership – OSHA’s safety and health program audit tool lists out seven critical elements that sum up workplace safety. But how exactly can organizations enforce processes to ensure safe productivity across the workplace? The answer lies in conducting thorough safety audits and risk resolutions.
Identify the Risks
Your employees spend a large chunk of their day within the workplace environment you design for them. To ensure their safety and well-being, it is critical to detect any risks that may be lingering in your workplace procedures and processes. A great place to start would be to ask questions like:
- Are all hazards marked with tags and signage?
- Does the workplace have proper ventilation?
- Are all commercial vehicles (if you deploy any) well maintained?
Workplace safety standards vary with every organization. Whether you’re operating in the automobile industry or have a fashion retail store – make sure you observe the type of workplace your organization has and spot and mend any element that might scream “risk.”
Put a Thorough Set of Policies and Procedures in Place
Before kickstarting your safety, it is important to put comprehensive safety procedures, policies, and protocols (authorized by executive management) in place. These policies must be implemented, communicated, analyzed, and updated bi-annually or annually. A great way to enforce and encourage your company’s safety standards would be through incentives. Aside from rewards, make sure you also deploy discipline programs that will inspire staff members to march toward safe productivity.
Set Emergency Procedures in Place
No company is immune to workplace accidents regardless of the number of safety protocols you have in place. What determines the strength of a company’s safety program is the way it responds to these incidents. Tap into your training program to educate staff members and supervisors on how to respond when emergencies arise. Place preventive equipment throughout the workplace and make it easily accessible to employees when the time comes.
Document every detail of the incident to detect indicators that might otherwise go unnoticed. Finally, have this documentation reviewed by a knowledgeable team to determine the weak points and take necessary action to avoid them from reoccurring.
Deploy Hazard Identification Systems
Analyzing incidents that may have occurred in the past can unveil several locations and patterns of hazards. It could be a slippery floor, or perhaps a misaligned set of stairs. Use the pattern of previous incidents to determine risk areas and put a “safety patch” on them. Sometimes, when the risks fail to be erased, auditors typically assign the task of safety maintenance to a staff member. It could range from picking up any packages lying on the ground to making markings on the floor to alert everyone about a potential hazard.
Train Staff to Use Personal Protective Equipment (PPE)
Here’s a fact: Using PPE (personal protective equipment) is all it takes to keep most workplace hazards at bay (this point was drilled into organizations during the COVID-19 pandemic). Train your personnel to use it efficiently and let them know where to find it when an emergency knocks at the door. Ask yourself, “Does my workplace have on-site PPE?” “Is it used regularly?” “Are there signages in place to alert staff members when they enter spaces that require PPE?” “Does your organization offer incentives for using it?” “Are there penalties for not using it?”
Lessons from the pandemic revealed that a minority of employees would resist the use of PPE and intentionally use it incorrectly (e.g. tucking a mask under your nose). Time and time again, it came down to the tone set by supervisors and middle management as to whether or not this continued. One supervisor choosing to avoid a confrontation with one employee for not wearing their PPE correctly only encourages others to defy safety mandates. Training supervisors in safety enforcement and holding them accountable can go a long way in improving a workplace’s safety.
Risk-Proof Heavy Tools and Machinery
Does your organization regularly deploy heavy machinery, industry-specific tools, forklifts, trucks, 4-wheelers, and other commercial vehicles? Do your power tools meet all industry standards? Make sure you ensure they are regularly maintained to establish a safe work environment. Your personnel must have access to all manufacturer’s manuals for every piece of equipment they use. In addition, they must be well-trained to use specific equipment and machines.
Offer Comprehensive Safety Training
Training can make all the difference between a safe workplace environment and a space infested with risks and hazards. Sketch a comprehensive and engaging training program to educate staff members about their workplace, and how they can safely perform their duties, avoid getting injured during work, and remain fully productive. Deploy varying shades of training including computer-based programs, group training sessions led by an instructor, roleplay, quizzes, and more to ensure efficiency, engagement, and retention. Remember, training must be ongoing and not just reserved for new hires.
In a gist, a well-rounded safety training would include, recognizing and communicating a hazard, following company safety protocols, setting reporting mechanisms, restricted behaviors, thorough PPE standards, and control measures. There should be additional training for supervisors and managers on the enforcement of safety rules.
Measure and Analyze the Metrics
Having a comprehensive set of parameters may be critical for workplace safety. However, the only way to ensure they bring real results is by consistently reviewing them. Here are a final set of questions to consider when designing a compliant workplace devoid of risks:
- How are the metrics this quarter? Are they better than the ones in the past? Is your organization meeting its safety goals?
- Which patterns of accidents are the most visible? Which issues must be resolved immediately?
- How effectively are hazards being analyzed? Who is identifying them? Which areas see the most risks? Are all high-risk areas managed by the same supervisor?
- Are employee training levels up to the mark? Which supervisors need to catch up? Which workers must put in more work?
To resolve the above questions efficiently, it is critical to establish a set of standards that are trackable, objective, and measurable. Review past accidents and put new protocols in place to keep similar issues at bay. Finally, maintain an organized record of incidents, training, and inspection and compare progress at periodic intervals.